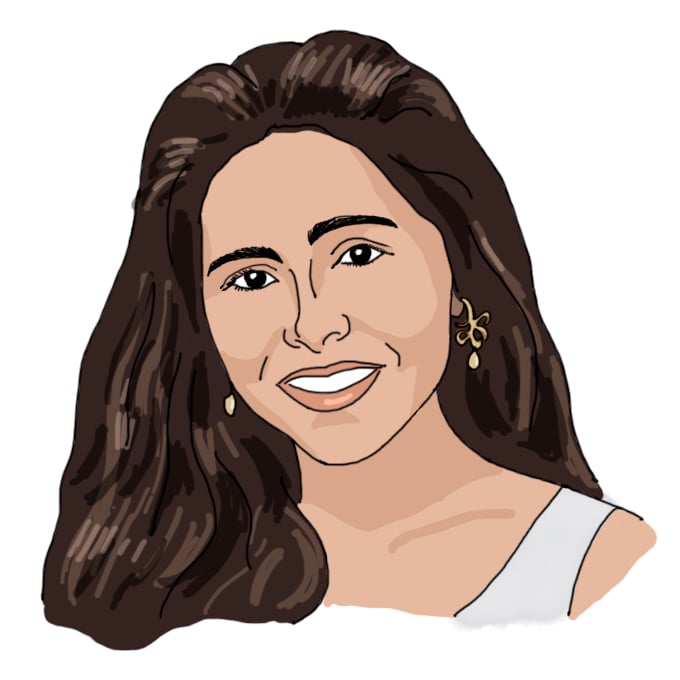
just do it by Amber V. '24
don’t say you’re gonna do it!
Let’s meet the CNC mill. This one is called HAAS. He’s proven useful in 2.008, a meche class known for its final project: to manufacture 50 yo-yos.
Mills can cut in 3 directions, (X, Y, Z), which makes them useful for cutting shapes into metal. In this case, we’re talking about molds for the plastic pieces of our yo-yo. I’ll make a blog on the yo-yo making process in full some time down the road. This blog is about CAM — Computer-Aided Manufacturing, or making the mill run automatically.
A year and many days ago, I shuffled into LMP01 Don’t ask me what this stands for because I don’t remember and it’s kind of silly. It’s a basement makerspace with lotsa big machines in a typical sleep-deprived stupor. Arcturus had scheduled a lesson on the CNC02 Computerized Numerical Control: an automated mill. I use this word as a noun and a verb (CNC: to cut out a part on the CNC mill) with the LMP instructors. I would later learn that Wade and Josh are some of my favorite lecturers in MechE, but on that day, I could barely stay awake on my feet. Handling a mill was difficult, but automating the process seemed many times more so.
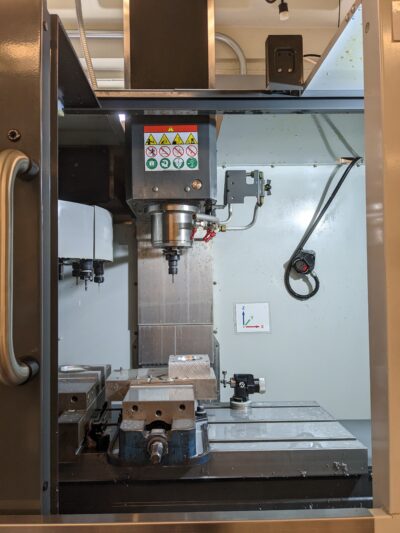
CNC front view
That spring, I took a class that showed me lots of new engineering skills, including using a wood CNC. I procrastinated drawing up a CAM03 Computer-aided manufacturing, essentially telling the computer what toolpaths to take. model for, uh, weeks. I eventually got one in, but by then I was too hosed to go and machine the part.
So I came to 2.008, Manufacturing and Design II, without any practical CAM or CNC experience. I thought I was an outlier until we started planning our final project, and a senior teammate said, “Yeah, I’m gonna learn CAM.”
As it turns out, we would all have to learn CAM. Manufacturing a yo-yo is fairly complicated. We’re injection-molding each plastic piece individually, and our yo-yo has 5 plastic pieces, meaning 1004 actually way, way more, because we keep iterating on the design and re-making some of the parts mold halves to CAD, CAM, and CNC. We split the work between the five of us.
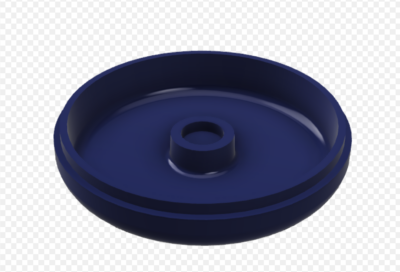
3-D render of half the yo-yo body
The night before my first mold CAM was due, I came back from B1 fight club05 exactly what it sounds like. around 1am, opened my laptop, and set to work. I stared at Fusion for a while, then stared at a Canvas tab, and switched back and forth for a while.
Eventually I pulled up Wade’s step-by-step CAM tutorial from 2.008 lecture. I’ve never had a CAM lesson that penetrated before, but seeing his screen on a recording allowed me to go back and see every mouse-click, which was actually so useful. By now it was 2 am. I was in a good mood from fight club, despite having been beaten up, and I wanted more than anything to go to sleep.
So I went between the tutorial and my Fusion design, adding toolpaths and running simulations. A 9 am deadline makes crazy things happen. By 4 am, the CAM was done.
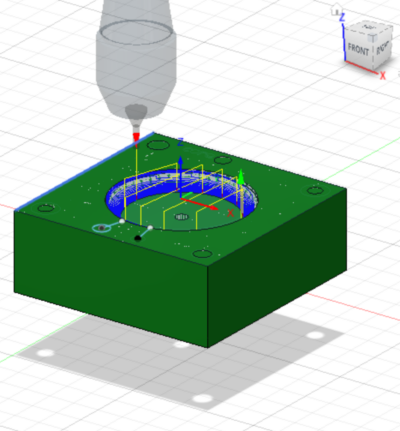
CAM pathway showing an endmill toolpath (yellow) as it cuts the sides of the mold (blue)
The next day I felt mostly deceased, but I came to 2.008 lab and stayed awake this time as Josh taught us how to use the CNC. Its blades are enclosed in a big cage, and the machine will only run when the doors are shut, protecting human hands from spinning blades. The anxiety around running a CNC machine stems from the CNC tools being expensive. Bad instructions can cause it to break a tool and wreck your piece.
But I was too sleep-deprived to feel much anxiety. The atmosphere was relaxed as all five of us gathered around the machine. One of my teammates volunteered to run the CNC first, under Josh’s instruction. He kept testing the limits of how fast the machine could go.
We needed to finish the other half of the mold at open lab time during the week. I had taken on less work the first week, so I volunteered.
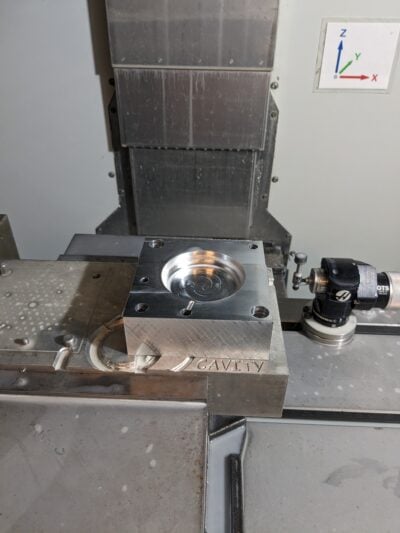
finished mold clamped in the machine
I came in to lab. A group of students were gathered around the lathe. Some grad students were stationed by the waterjet.06 cuts metal with a jet of water I set up at the CNC. I asked for some pointers, then loaded the CAM program and moved carefully through the set-up. The machine whirred to life. It began to spray foul-smelling coolant on the piece. A spinning endmill07 like a drill bit, but it can also cut sideways faced the part down.
I sat there, my hand over the stop button in case something went wrong. That’s the standard practice: you sit by the machine as it runs, always ready to step in. I thought about how much CAM and CNC had intimidated me once. Now my biggest worry was the machine finishing the process cut before I had to go to lab.
You just do it. Or you put yourself in classes that will make you do it. It will come due, and then it will be done.
Here’s the finished mold. We’re injection-molding the plastic yo-yo body next.
- Don’t ask me what this stands for because I don’t remember and it’s kind of silly. It’s a basement makerspace with lotsa big machines back to text ↑
- Computerized Numerical Control: an automated mill. I use this word as a noun and a verb (CNC: to cut out a part on the CNC mill) back to text ↑
- Computer-aided manufacturing, essentially telling the computer what toolpaths to take. back to text ↑
- actually way, way more, because we keep iterating on the design and re-making some of the parts back to text ↑
- exactly what it sounds like. back to text ↑
- cuts metal with a jet of water back to text ↑
- like a drill bit, but it can also cut sideways back to text ↑